Views: 371
If you have any recommendation please let us know 如果您有好的建议请告诉我们。
Please click here for more Lean books written in Chinese or billingual. 请点击这里展开更多中文精益书籍。
Lean 精益
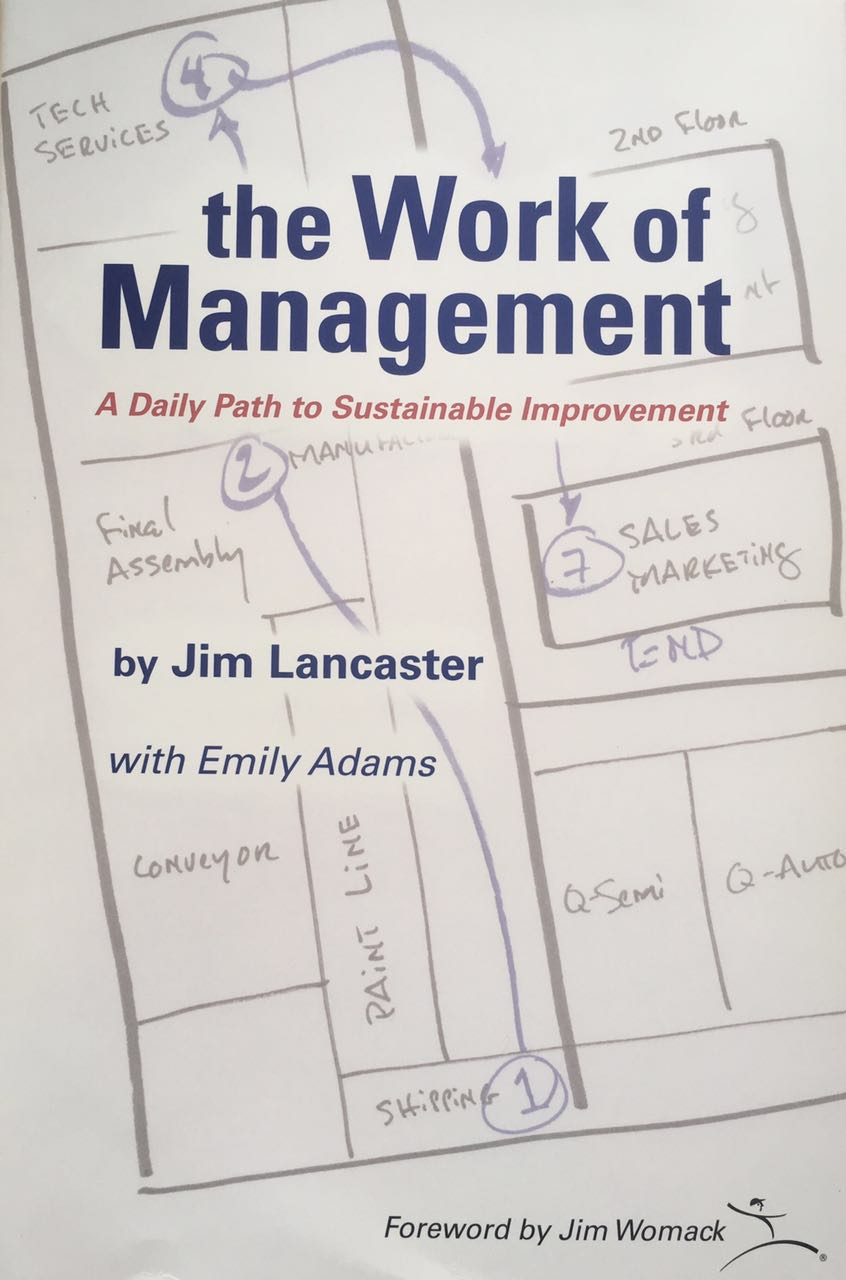
the Work of Management: A Daily Path to Sustainable Improvement
by Jim Lancaster (Author), Emily Adams (Editor), Jim Womack (Foreword)
Basic Information 基本信息
$35
Hardcover: 171 pages
Publisher: Lean Enterprise Academy Ltd; 1st edition (January 1, 2017)
Language: English
ISBN-10: 1934109029
ISBN-13: 978-1934109021
Package Dimensions: 9.1 x 6.4 x 0.9 inches
Shipping Weight: 2.5 pounds
Basic Information 基本信息
$10
Format: Kindle Edition
File Size: 7378 KB
Print Length: 215 pages
Publisher: Lean Enterprise Institute Inc. (3 July 2017)
Sold by: Amazon Asia-Pacific Holdings Private Limited
Language: English
ASIN: B073PZSKG3
Contents 内容
Author and CEO Jim Lancaster tells a practical and inspiring story on two levels. It’s a close-up, candid look at his personal transformation as a leader. It’s also a practical, in-depth, business case study of Lantech’s lean transformation, relapse, and comeback that American manufacturing – and other industries – can use to profitably transform themselves. In his engaging story, Lancaster reveals: Why Lantech, a stellar lean performer for a decade, struggled over time (like many other companies) to sustain gains and improve financial performance. Why 60 to 90 minutes of daily frontline management activities are a CEO’s most important minutes of the day for sustaining and growing their business. 8 steps executives can take to lead experiments to create a bullet-proof, real-time daily management system without expensive consultants. Why daily management requires a major shift in managers’ mindsets and behaviors from giving orders and judging individuals on performance to asking questions and enabling good work by people at lower levels so metrics are routinely met. How daily management and sustainable continuous improvement produces dramatic positive effects on the bottom line. What happens in daily huddles where team members review how well they are sustaining gains and staying on track. How to practice true lean leadership in which “bosses” truly act like coaches — not solving problems for people but asking them what they can to do help. How Lantech ties together all facets of the company in an integrated way (from sales to production). Why it deeply invests in the lean training and practice of every single employee every day.
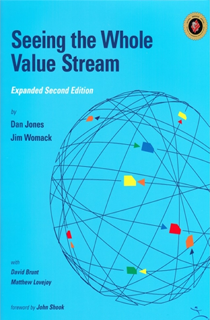
Seeing the whole value chain
by James P. Womack and Daniel T. Jones
Basic Information 基本信息
$90
Spiral-bound
Publisher: Lean Enterprises Inst Inc (1900)
ASIN: B00ZVPAAHM
Basic Information 基本信息
RMB 250
Format: Kindle Edition
File Size: 6086 KB
Print Length: 108 pages
Publisher: Lean Enterprise Institute, Inc.; 2 edition (19 August 2012)
Sold by: Amazon Asia-Pacific Holdings Private Limited
Language: English
ASIN: B00908ELHG
Contents 内容
An expanded 2nd edition of the workbook Seeing the Whole
When the first edition of Seeing the Whole was published in 2003, the world was in a mad rush to outsource and offshore in pursuit of suppliers with drastically lower piece prices. Today the situation is very different; currencies have shifted, labor costs in many low-wage countries have risen, and the potential for squeezing further price reductions from suppliers is largely exhausted. What’s more, high product quality and rapid response to changing customer demands have proved elusive along unwieldy, opaque supply chains. Seeing the Whole Value Stream provides managers with a proven method for understanding and improving the value-creating process that suppliers share with customers.
By identifying all the steps and time required to move a typical product from raw materials to finished goods, the authors show that nearly 90 percent of the actions and 99.9 percent of the time required for the supply chain’s current state create no value. In addition, the method clearly shows demand amplification of orders as they travel up the supply chain, steadily growing quality problems, and steadily deteriorating shipping performance at every point up stream from the customer.
Applying the method to a realistic example, the authors show how four firms sharing a value stream can create a win-win-win-win future in which everyone, including the end consumer, can be better off.
The workbook goes step-by-step through an improvement process that converts the traditional supply chain of isolated, compartmentalized operations into an ideal future-state value stream in which value flows from raw materials to customer in just 6 percent of the time previously needed. The dramatically improved value stream also eliminates unnecessary transport links, inventories, and handoffs, the key drivers of hidden connectivity costs.
The information in the 108-page book is supported by multiple diagrams, charts, and maps. The main sections of the book are:
– Getting Started
– The Current-State Map
– The Extended Value Stream
– Future States 1 & 2
– Ideal State
– Perspectives on Extended Value Streams: 5 essays
In response to feedback asking for examples in other sectors and questions about how to understand supply chain costs more accurately, five essays have been added to the book for this new edition. These essays demonstrate how real companies have taken on the challenge of improving their extended value streams working in collaboration with their suppliers and customers.
The new essays for the book are:
– Spreading value-stream thinking from manufacturers to final customers through service providers—extending the wiper example. This extends the value-stream analysis in the first edition—using the same example of a windshield wiper—through the auto service system to the end customer.
– Applying extended value-stream thinking to retail—a look at the Tesco story. This follows the path of an individual product through a complex retail channel from manufacturer to end customer.
– Learning to use value-stream thinking collaboratively with suppliers and customers. This essay demonstrates how a second-tier supplier convinced much larger partners to embrace collaborative thinking about their shared value stream.
– Product costing in value-stream analysis. An essay on adding realistic costing to value streams to more accurately understand total cost.
– Seeing and configuring the global value stream. This essays shows how a manufacturer can analyze all of the value streams in a complex supply network.
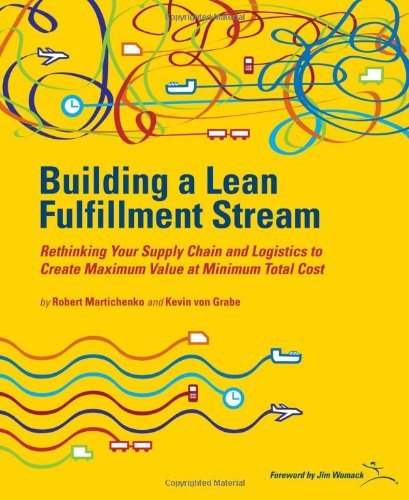
Building a Lean Fullfillment Stream
By Robert Martichenko
Basic Information 基本信息
$75
Spiral-bound
Publisher: Lean Enterprises Inst Inc (May 25, 2010)
ASIN: B00N4F9GL2
Contents 内容
Building a Lean Fulfillment Stream will change the way you think about your supply chain and logistics networks. Even better — it gives you a way to act using lean principles to transform and continuously improve these two key flows. In this pioneering workbook, lean logistics veterans Robert Martichenko and Kevin von Grabe explain step-by-step a comprehensive, real-life implementation process for optimizing your entire fulfillment stream from raw materials to customers, including practical insights into two critical concepts: calculating the total cost of fulfillment and collaborating across all functions and firms along the fulfillment stream. Your company, like most, probably calculates costs at different points within departments, such as the piece price paid by the purchasing department to a supplier. Few companies figure the total cost associated with each major function across the whole fulfillment stream. Calculating total cost, which most executives find surprisingly large, lets you measure the impact of your improvement efforts on operational performance and overall income. Martichenko and von Grabe also give you guidance and tools for collaboration. Using the example company ABE Corp. as their model, the authors illustrate how the lean conversion process is a win-win for every company along the supply chain. And an accompanying analysis illustrates the financial benefits and shows you how to apply the metrics. The narrative, supported by 41 charts and illustrations, including value-stream maps, shows you:How to apply the eight guiding principles for implementing lean fulfillment, even when all the data and variables are not known.
The seven major types of waste in logistics and supply chains.
How a fulfillment-stream council of representatives from internal departments, customers, suppliers, and transportation providers gives critical guidance and support.
The “eight rights” for assessing perfect order execution.
What lean metrics to use, such as why average days on hand of inventory is a better measure than inventory turns.
How to identify and eliminate waste in shipping, receiving, and yard management.
Learn how to use lean management principles to convert supply chains and logistics networks into smooth, fast-flowing fulfillment streams.About the Authors: Robert Martichenko
Robert began his lean journey working at Toyota Motor Manufacturing Indiana and has over 15 years of lean supply chain and third-party logistics experience. He sits on the editorial advisory board of Logistics Quarterly magazine and is a trained six sigma black belt. A past president of the Cincinnati Council of Supply Chain Management Professionals (CSCMP) roundtable, he now serves as a regional advisor to a group of CSCMP roundtables. He recently co-authored the business management book Lean Six Sigma Logistics. Robert also wrote the leadership handbook Success in 60 Seconds and the lean primer Everything I Know About Lean I Learned In First Grade. Robert also teaches global business at Saint Louis Universitys John Cook School of Business. Kevin von Grabe
Kevin has focused his career on materials management, transportation, consulting and third party logistics. This experience includes multiple operational launches, including the “green field” start up at Toyota Motor Manufacturing Indiana. Kevin’s experience has provided him with several international experiences. These include operational start ups for Jabil Circuit at green field and brown field manufacturing plants in both Hungary and China. Kevin complements his years of logistics experience with a Bachelors Degree in Logistics Management from Central Michigan University. Born in Detroit Michigan, Kevin currently resides in Kentucky with his wife Jeanette and son Kirk.
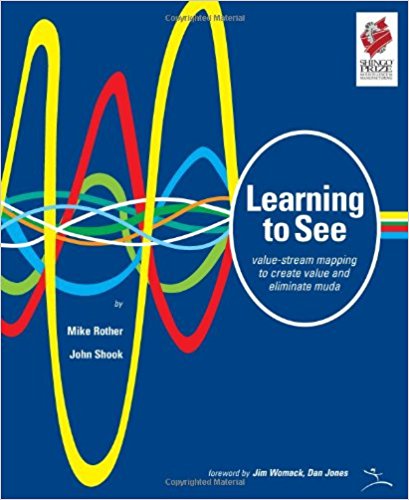
Learning to See: Value Stream Mapping to Add Value and Eliminate MUDA
by Mike Rother (Author), John Shook (Author), Jim Womack (Foreword), Dan Jones (Foreword)
Basic Information 基本信息
$60 ISBN-13: 978-0966784305ISBN-10: 0966784308
Contents 内容
The journey towards lean is difficult and strewn with uncertainties. Where do you begin? What are the nonvalue-adding processes that can be eliminated? What lean techniques should you apply, where, and in what order? These are difficult questions to answer if you dont have the proper tool.
More and more companies are using value-stream mapping to find the answers. When you are ready to apply this fundamental tool in your company, there is no better resource than Learning to See, the workbook that introduced the mapping technique in the summer of 1998 and has been translated into 11 languages. Mapping is an overarching tool that gives you a picture of the entire production process, including both value and nonvalue-adding activities. It helps you avoid the common mistake of cherry-picking lean techniques, which leads to building isolated islands of improvement instead of improving the whole production flow to reap the biggest benefits. And mapping helps you understand the sources of waste so you can apply the right lean techniques at the right places for bigger and more sustainable impact. The benefits of mapping also include:
·Establishing a direction for the companys improvement efforts – maps become the blueprints for the lean transformation.
·Gaining a better understanding of the linkages between material and information flow.
·Visualizing improvements to the overall production flow, instead of spot improvements to single processes.
·Creating the basis of an effective lean implementation plan by designing how the door-to-door material and information flow should operate.
·Giving operators, engineers, and managers a common language of continuous improvement.
Beginning with a foreword by Jim Womack and Dan Jones, authors of the landmark book Lean Thinking, the Learning to See workbook breaks down the important concepts of value-stream mapping into an easy-to- understand format. The 102-page workbook is filled with actual value-stream maps, as well as engaging diagrams and illustrations. Like all LEI workbooks,Learning to See is written in plain English and answers the key question managers often have about lean tools and concepts -What do I do on Monday morning to implement this?Simple and Practical
Youll learn how to see value, differentiate value from waste, and eliminate the sources of waste by creating accurate current-state and future-state maps for each of your product families. And youll learn the reasons for introducing a mapping program and how it fits into a lean conversion. Throughout the process, Learning to See explains the key concepts of value-stream mapping. Written by experienced lean practitioners, Mike Rother and John Shook, the workbook makes complicated concepts simple. To encourage you to become actively involved in the learning process, Learning to See contains a case study based on a fictional company called Acme Stamping. Youll begin by mapping the current-state of a value stream and identifying all the sources of waste in it. After the waste is identified, you develop a map of a leaner future value stream and an action plan for implementation. The authors guide you through the process of designing a leaner future-state by using eight simple but practical questions:
1.What is the takt time?
2.Will you build to a finished goods supermarket, or directly to shipping?
3.Where can you use continuous flow processing?
4.Where will you need to use supermarket pull systems to control production of upstream processes?
5.At what single point in the production chain (the “pacemaker process”) will you schedule production?
6.How will you level the production mix at the pacemaker process?
7.What increment of work will you consistently release and take away at the pacemaker process?
8.What process improvements will be necessary for the value stream to flow as your future-state design specifies?
The workbook also shows you how to break the future-state implementation process into do-able steps and how to develop a yearly value-stream improvement plan. It features a set of data for a second example company so you can practice mapping, and then compare your maps to the ones provided in the appendix. The appendix also features a list of icons and their usages for reference. Learning to See is for managers and executives who are familiar with basic lean concepts as described in Lean Thinking by Womack and Jones.
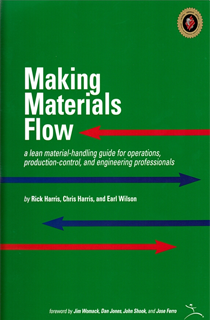
Making Materials Flow: Volume 1.1: A Lean Material-handling Guide for Operations, Production-control, and Engineering Professionals
by Rick Harris (Author), Chris Harris (Author), Earl Wilson (Author)
Basic Information 基本信息
$85
Spiral-bound
Publisher: Lean Enterprise Institute,US; Spi edition (1 July 2011) (1600)
ASIN: B011T7NJX2
Basic Information 基本信息
RMB 900
Spiral-bound: 94 pages
Publisher: Lean Enterprise Institute,US; Spi edition (1 January 2003)
Language: English
ISBN-10: 0974182494
ISBN-13: 978-0974182490
Product Dimensions: 1.3 x 22.9 x 27.3 cm
Contents 内容
The Making Materials Flow workbook from the Lean Enterprise Institute (LEI) shows manufacturing professionals in operations, production control, and industrial engineering how to replace material-handling systems designed for mass production with systems that support lean production.
“Companies are making progress in creating areas of continuous flow as more managers learn about value-stream mapping and continuous-flow cells,” said Rick Harris, co-author of the new Making Materials Flow workbook. “But as I walk through facilities and examine earnest efforts to create continuous flow, I see how hard it is to sustain steady output. The problem often is the lack of a lean material-handling system for purchased parts to support continuous-flow cells, small-batch processing, and traditional assembly lines.” Making Materials Flow uses plain language and illustrations to explain how to create, sustain, and improve a lean material-handling system for purchased parts. It is designed to stop the erratic output, wasted time, excess costs, and exhausting human effort caused by trying to supply lean production processes with traditional material-handling systems. Making Materials Flow, which received a 2005 Shingo Research Prize, shows you how to apply the relevant concepts and methods in a step-by-step progression. The workbook reveals the exercises, formulas, standards, and forms that a consultant would use to implement the system in your environment. And, like LEI’s other workbooks, Making Materials Flow answers the key question managers often have about lean tools and concepts, “What do I do on Monday morning to implement this?”The key implementation steps detailed in the workbook include:
·Developing the Plan For Every Part (PFEP). This basic database fosters accurate and controlled inventory reduction and is the foundation for the continuous improvement of a facility’s material-handling system.
·Building the purchased-parts market. Learn the formulas and methods to size and operate a market that eliminates the waste of hoarding, searching for parts, and storing inventory throughout a facility.
·Designing delivery routes. You get the principles and calculations that turn a sprawling, messy plant into an organized community where operators get the parts they need, when needed, and in the quantity needed, delivered right to their fingertips ·Proper delivery routes not only improve inventory and flow but also safety and housekeeping.
·Implementing pull signals. Learn four steps to creating a system that keeps inventory under control by allowing operators to pull just what they need while focusing on producing value for customers. You’ll also lean how to calculate the number of pull signals needed and how often to deliver material.
·Continuously improving the system. Systematically pursue perfection by implementing periodic audits of the material-handling system across all levels from route operator to plant manager. You’ll learn the five-step process for introducing audits of the market, routes, and pull signals by a cross-functional team from production control, operations, and industrial engineering.
Harris and co-authors Chris Harris and Earl Wilson break down the implementation process by leading you through 10 simple but pragmatic questions:The Plan For Every Part (PFEP)
1.What information should you include in the PFEP?
2.How will you maintain the integrity of the PFEP?
Developing a Purchased-Parts Market
1.Where do you locate your purchased-parts market?
2.What is the correct size for your purchased parts market, and what is the correct amount of each part to hold in the market?
3.How do you operate your purchased-parts market?
Designing the Delivery Route and the Information Management System
1.How do you convey parts from the purchased-parts market to the production areas?
2.How do your production areas signal the purchased-parts market what to deliver and when?
3.How do you fill the delivery route?
Sustaining and Improving
1.How can you sustain the performance of your lean material-handling system?
2.How can you identify and remove additional waste?
An appendix explores how to adapt the principles of lean material-handling to different environments, such as incorporating work-in-process (WIP) markets into the system, adding delivery routes from production cells to a finished-goods market, and applying the system to low-volume, high-mix processes. Making Materials Flow will help lean leaders, managers, and executives in production control, operations, and engineering who have at least a basic knowledge of lean concepts such as value-stream mapping, cell design, and standard work. For information on the Making Materials Flow workshop, click on the Training tab above.
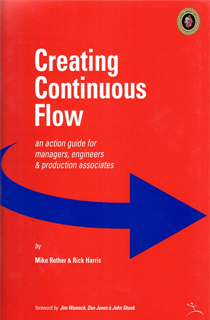
Creating Continuous Flow: An Action Guide for Managers, Engineers and Production Associates
by Mike Rother (Author), Rick Harris (Author)
Basic Information 基本信息
$ 50
Spiral-bound: 103 pages
Publisher: Lean Enterprise Institute; Version 1.0, June 2001 edition (December 1, 2001)
Language: English
ISBN-10: 0966784332
ISBN-13: 978-0966784336
Product Dimensions: 0.5 x 9.2 x 10.8 inches
Shipping Weight: 1.3 pounds
Basic Information 基本信息
Kindle Edition: RMB 300
Format: Kindle Edition
File Size: 9418 KB
Print Length: 105 pages
Publisher: Lean Enterprise Institute, Inc. (14 August 2013)
Sold by: Amazon Asia-Pacific Holdings Private Limited
Language: English
ASIN: B00EKPE7IW
Contents 内容
This workbook explains in simple, step-by-step terms how to introduce and sustain lean flows of material and information in pacemaker cells and lines, a prerequisite for achieving a lean value stream.
A sight we frequently encounter when touring plants is the relocation of processing steps from departments (process villages) to product-family work cells, but too often these “cells” produce only intermittent and erratic flow. Output gyrates from hour to hour and small piles of inventory accumulate between each operation so that few of the benefits of cellularization are actually being realized; and, if the cell is located upstream from the pacemaker process, none of the benefits may ever reach the customer.
This sequel to Learning to See (which focused on plant level operations) provides simple step-by-step instructions for eliminating waste and creating continuous flow at the process level. This isn’t a workbook you will read once then relegate to the bookshelf. It’s an action guide for managers, engineers, and production associates that you will use to improve flow each and every day.
Creating Continuous Flow takes you to the next level in work cell design where you’ll achieve even greater cost and lead time savings. You’ll learn:
– where to focus your continuous flow efforts
– how to create much more efficient work cells and lines
– how to operate a pacemaker process so that a lean value stream is possible
– how to sustain the gains, and keep improving
Creating Continuous Flow is the next logical step after Learning to See. The value-stream mapping process defined the pacemaker process and the overall flow of products and information in the plant. The next step is to shift your focus from the plant to the process level by zeroing in on the pacemaker process, which sets the production rhythm for the plant or value stream, and apply the principles of continuous flow.
Every production facility has at least one pacemaker process. The pacemaker processes is usually where products take their final form before going to external customers. It’s called the pacemaker because how you operate here determines both how well you can serve the customer and what the demand pattern is like for your upstream supplying processes.
How the pacemaker process operates is critically important. A steady and consistently flowing pacemaker places steady and consistent demands on the rest of the value stream. The continuous flow processing that results allows companies to create leaner value streams.
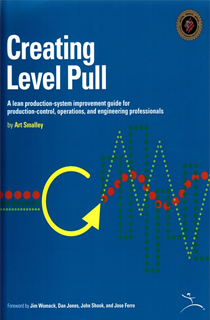
Creating Level Pull (Lean Tool Kit)
by Art Smalley (Author)
Basic Information 基本信息
$60
ISBN-13: 978-0974322506ISBN-10: 0974322504
Basic Information 基本信息
RMB 250
Spiral-bound: 114 pages
Publisher: Lean Enterprise Institute,US (1 January 2004)
Language: English
ISBN-10: 0974322504
ISBN-13: 978-0974322506
Product Dimensions: 1.9 x 24.1 x 27.3 cm
Contents 内容
The Creating Level Pull workbook from the Lean Enterprise Institute (LEI) shows readers how to advance a lean transformation from a focus on isolated improvements to improving the entire plantwide production system by implementing a lean production control system.
“The workbook is unique because it is a step-by-step case study on how to implement a level, pull-based production control system,” said author Art Smalley. “This is a new step towards ‘system kaizen’ that is not yet well understood outside of Toyota.”
The lean efforts at most companies focus on “point kaizen” (e.g., reducing set up times, implementing 5S, etc.) that improves a small portion of the value stream running from raw materials to finished products. Or they focus on “flow kaizen” that improves the entire value stream for one product family. Creating Level Pull shows how companies can make the leap to “system kaizen” by introducing a lean production control system that ties together the flows of information and materials supporting every product family in a facility. With this system in place, each production activity requests precisely the materials it needs from the previous activity and demand from the customer is leveled to smooth production activities throughout the plant. “A truly lean production-control system that rigorously controls production at every step and levels demand from the customer has proved a great challenge for most firms,” said James Womack, LEI president and founder, “but Art gives you all the knowledge needed to succeed.” Using a realistic example facility, Smalley shows readers how to make the transition to a robust pull system. This involves answering a series of 12 critical questions including what items to hold in finished goods inventory and what items to make to order, how to buffer the system against instability, how to schedule batch processes, and how to level the production schedule. Careful attention to leveling (called heijunka) permits facilities to accommodate variations in demand with minimum inventories, capital costs, manpower, and production lead time. Like all LEI workbooks, Creating Level Pull walks readers through the implementation process using a clear step-by-step progression. The 115-page workbook includes scores of illustrations that help explain all the key steps and formulas. Smalley was one of the first foreigners made a permanent employee of the Toyota Motor Corporation in Japan, assisting with the startup of Toyota facilities in the U.S. and other countries. He subsequently was Director of Lean Production Operations at Donnelly Corporation and manager of the Production System Design Center at McKinsey and Company. The main sections of the workbook are:
·Getting Started
·Guarding Against Demand Surges and Production Shortfalls
§ Which products should you hold in a finished goods inventory, and which products should you produce only to a confirmed order?
§ How much of each product should you hold in finished goods?
§ How will you organize and control the finished-goods store?
·Creating the Pacemaker
§ At what single point will you schedule the value stream?
§ How will you level production at the pacemaker?
§ How will you convey demand to the pacemaker and finished goods from the pacemaker?
·Controlling Production Upstream
§ How will you manage information and material flow upstream from the pacemaker?
§ How will you size your markets and trigger withdrawal pull?
§ How will you control batch processes upstream from the market?
·Expanding the System
§ How will you expand the level pull system across the facility?
·Sustaining and Improving
§ How will you sustain your level pull system?
§ How will you improve your level pull system?
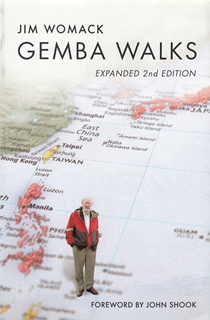
GEMBA WALKS
by James P Womack (Author),John Shook (Foreword)
Basic Information 基本信息
$30
Paperback: 311 pages
Publisher: Lean Enterprise Institute, Inc.; 2nd ed. edition (January 1, 2013)
Language: English
ISBN-10: 193410938X
ISBN-13: 978-1934109380
Product Dimensions: 6 x 1 x 8.9 inches
Basic Information 基本信息
RMB 100
Paperback: 340 pages
Publisher: Lean Management Institute of India; Expanded Second Edition edition (2014)
Language: English
ISBN-10: 9384390011
ISBN-13: 978-9384390013
Product Dimensions: 22.4 x 14.9 x 2.3 cm
Contents 内容
Gemba Walks is Jim Womacks newest book, a collection of letters and essays. It is also available as an e-book from Apple, Amazon or Amazon.co.uk or Amazon.de, Barnes & Noble, and Google. “The life of lean is experiments. All authority for any sensei flows from experiments on the gemba [the place where work takes place], not from dogmatic interpretations of sacred texts or the few degrees of separation from the founders of the movement. In short, lean is not a religion but a daily practice of conducting experiments and accumulating knowledge.” So writes Jim Womack, who over the past 30 years has developed a method of going to visit the gemba at countless companies and keenly observing how people work together to create value. Over the past decade, he has shared his thoughts and discoveries from these visits with the Lean Community through a monthly letter. With Gemba Walks, Womack has selected and re-organized his key letters, as well as written new material providing additional context. Gemba Walks shares his insights on topics ranging from the application of specific tools, to the role of management in sustaining lean, as well as the long-term prospects for this fundamental new way of creating value. Reading this book will reveal to readers a range of lean principles, as well as the basis for the critical lean practice of: go see, ask why, and show respect. Womack explains: why companies need fewer heroes and more farmers (who work daily to improve the processes and systems needed for perfect work and who take the time and effort to produce long-term improvement)
how “good” people who work in “bad” processes become as “bad” as the process itself
how the real practice of showing respect comes down to helping workers frame and solve their own problems
how the short-term gains from lean tools can be translated to enduring change from lean management.
how the lean manager has a “restless desire to continually rethink the organization’s problems, probe their root causes, and lead experiments to test the best currently known countermeasures”
By sharing his personal path of discovery, Womack sheds new light on the continued adoption and development of the most important new business system of the past fifty years. His journey will provide courage and inspiration for every lean practitioner today. About the Author:Jim Womack
Management expert James P. Womack, Ph.D., is the founder of and senior advisor to the Lean Enterprise Institute, Inc., a nonprofit training, publishing, conference, and management research company chartered in August 1997 to advance a set of ideas known as lean production and lean thinking, based initially on Toyota’s business system and now being extended to an entire lean management system.Womack is also the co-author of Machine That Changed the World, Lean Thinking, Lean Solutions, and the LEI workbook Seeing the Whole. He received a B.A. in political science from the University of Chicago in 1970, a masters degree in transportation systems from Harvard in 1975, and a Ph.D. in political science from MIT in 1982. As research director of MIT’s International Motor Vehicle Program, Womack led the research team that coined the term “lean production” to describe the Toyota Production System.Womack served as the Institutes chairman and CEO from 1997 until 2010 when he was succeeded by John Shook
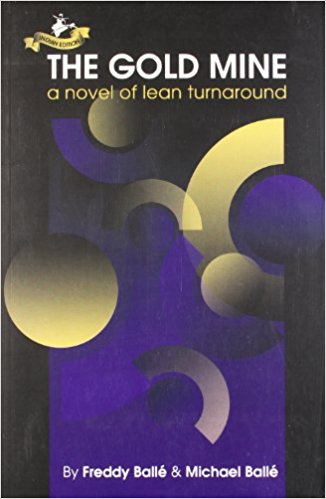
The Gold Mine : A novel of lean turnaround
by Freddy Balle (Author), Michael Balle (Author)
Basic Information 基本信息
$30
Paperback: 360 pages
Publisher: Lean Enterprises Inst Inc (May 30, 2005)
Language: English
ISBN-10: 0974322563
ISBN-13: 978-0974322568
Product Dimensions: 1 x 5.8 x 8.8 inches
Basic Information 基本信息
RMB 40
Paperback
Publisher: Penguin Books Ltd (2009)
Language: English
ISBN-10: 8190704001
ISBN-13: 978-8190704007
Package Dimensions: 22.8 x 15 x 1.6 cm
Contents 内容
The Gold Mine: a Novel of Lean Turnaround deftly weaves together the technical and human pieces of implementing lean manufacturing in an engaging story that readers will find both compelling and instructive. Authors Freddy and Michael Ballé have produced the first integrated and systematic approach to a set of ideas that have maximized value and minimized waste throughout the world. At the heart of the Gold Mine is Bob Woods, a curmudgeonly sensei coaxed out of retirement by his son Mike to help boyhood friend Phil Jenkinson save his struggling company. Despite terrific products and a backlog of orders, Phil’s company cannot generate enough cash from its operations to pay its bills. And so Mike enlists Bob to help his pal fix this crisis.
“You’re trying to deal with your mess as if it was a technical problem,” Bob tells Phil. “Move this machine here, change this design there, which it is to some extent, but … it’s all about people. You have a leadership problem not just a production or business problem.” As Phil begins to tackle the key challenges necessary to improve his company’s operations, he comes to understand the deeper points of lean. Readers will also draw powerful insights from his journey.
The Gold Mine presents all the key lean principles, ranging from well-known ideas such as pull and flow, to lesser-known yet equally important principles such as jidoka and heijunka. The book also reveals lean as a system—using a realistic story to show how the principles are interrelated and how they lead to useful tools such as kanban or 5S.
Editorial Reviews
From the Publisher
“The Gold Mine is the first book to comprehensively introduce all the lean tools by means of a vivid personal story showing how hearts and minds are won over, said publisher James Womack, LEI president and founder. “It will spark ah-ha’s from everyone who has been there and provide profound insight for those who are just getting started.”
“Reading The Gold Mine is like eavesdropping on a sensei dispensing gems to a client,” says co-publisher Daniel Jones, founder of the Lean Academy in the UK. “Readers, especially those individuals working on the shop floor, will gain revelation and inspiration by living through the experiences of the hero. Managers and executives just beginning a lean transformation will learn valuable insights about how to sidestep the technical and people problems that lay ahead. And experienced lean thinkers will discover fresh insights about overcoming resistance to change.”
From the Author
Our novelistic approach addresses one of the reasons that it’s so hard to find any workable lean “recipe,” which is that the tools, or at least their level of implementation, must be linked to the management’s lean maturity. For instance, we would argue that lean is fundamentally about rigorous problem solving and involving operators in kaizen. Fine. But in most working environments, if you start there, as most TQM or six sigma programs do, you will end up with disappointing results. People will get confused about which problems to solve, how to go about change, and what kind of attitude to adopt when dealing with resistance or recurring problems. In a factory it’s usually easier to start a lean program with the basics, such as seven wastes, 5S, red bins for quality, reducing batch sizes by increasing tool changeover, and moving progressively to eliminating variation in the operators’ work cycle.
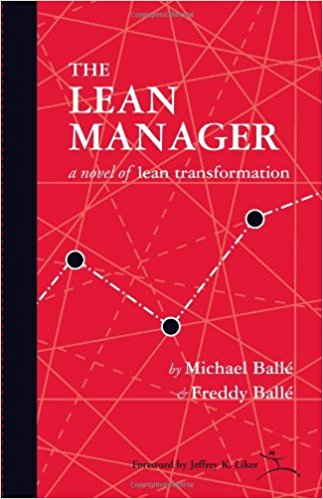
The Lean Manager: A Novel of Lean Transformation
by Freddy Balle (Author), Michael Balle (Author)
Basic Information 基本信息
$30
Paperback: 459 pages
Publisher: Lean Enterprises Inst Inc; 1 edition (July 29, 2009)
Language: English
ISBN-10: 1934109258
ISBN-13: 978-1934109250
Product Dimensions: 1.2 x 6 x 9 inches
Basic Information 基本信息
Kindle Edition: RMB 50
Paperback: 459 pages
Publisher: Lean Enterprise Institute,US (1 November 2009)
Language: English
ISBN-10: 1934109258
ISBN-13: 978-1934109250
Product Dimensions: 3.2 x 15.2 x 22.9 cm
Contents 内容
The Lean Manager: A Novel of Lean Transformation, by lean expertsMichael and Freddy Ball?, addresses the critical problem that mostcompanies face today: how can they advance beyond realizingisolated gains from deploying lean tools, to fundamentally changinghow they operate, think, and learn? The book gives companies adefinitive guide for sustaining their ability to learn and toimprove operations and financial performance, while continuallydeveloping people. “The only way to stay lean is to produce leanmanagers,” says Jim Womack, author, lean management authority, andLEI founder. “Every isolated effort will recede — or fail –unless companies learn to use the lean process as a way ofdeveloping individual problem-solvers with the ownership,initiative, and know-how to solve problems, learn, and coach newindividuals.” The Lean Manager, the sequel to the Ball?’sinternational bestselling business novel The Gold Mine, tells thecompelling story of plant manager Andrew Ward as he goes throughthe journey to becoming a lean manager. Under the guidance of PhilJenkinson (whose own lean journey was at the core of The GoldMine), Ward learns to use a deep understanding of lean tools, aswell as a technical know-how of his plant’s operations, to foster alean attitude that sustains continuous improvement. He learns howto use tools to unleash the creativity and motivation of people, sothey learn how to solve problems as well as coach and teach othersto solve problems. “I am excited and have hopes that this book willenlighten readers about what it really means to live a businesstransformation that puts customers first and does this throughdeveloping people,” said Jeffrey Liker, author of The Toyota Way.”People who do the work have to improve the work. There are tools,but they are not tools for ‘improving the process.’ They are toolsfor making problems visible and for helping people think about howto solve those problems.”
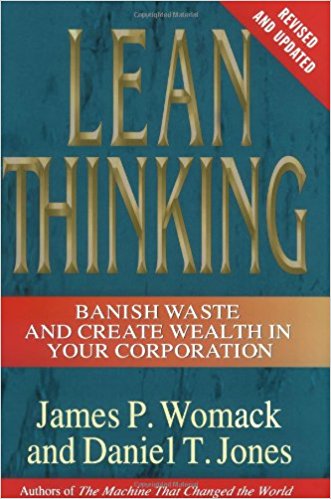
Lean Thinking: Banish Waste and Create Wealth in Your Corporation, Revised and Updated
by James P. Womack (Author), Daniel T. Jones (Author)
Basic Information 基本信息
$20
Hardcover: 396 pages
Publisher: Productivity Press; 2nd edition (June 1, 2003)
Language: English
ISBN-10: 0743249275
ISBN-13: 978-0743249270
Product Dimensions: 6.1 x 1.4 x 9.3 inches
Basic Information 基本信息
RMB 150
Hardcover: 400 pages
Publisher: Free Press; 2 Rev Upd edition (10 June 2003)
Language: English
ISBN-10: 0743249275
ISBN-13: 978-0743249270
Product Dimensions: 15.5 x 3.6 x 23.6 cm
Contents 内容
Expanded, updated, and more relevant than ever, this bestselling business classic by two internationally renowned management analysts describes a business system for the twenty-first century.
Expanded, updated, and more relevant than ever, this bestselling business classic by two internationally renowned management analysts describes a business system for the twenty-first century that supersedes the mass production system of Ford, the financial control system of Sloan, and the strategic system of Welch and GE. It is based on the Toyota (lean) model, which combines operational excellence with value-based strategies to produce steady growth through a wide range of economic conditions.
In contrast with the crash-and-burn performance of companies trumpeted by business gurus in the 1990s, the firms profiled in Lean Thinking — from tiny Lantech to midsized Wiremold to niche producer Porsche to gigantic Pratt & Whitney — have kept on keeping on, largely unnoticed, along a steady upward path through the market turbulence and crushed dreams of the early twenty-first century. Meanwhile, the leader in lean thinking — Toyota — has set its sights on leadership of the global motor vehicle industry in this decade.
Instead of constantly reinventing business models, lean thinkers go back to basics by asking what the customer really perceives as value. (It’s often not at all what existing organizations and assets would suggest.) The next step is to line up value-creating activities for a specific product along a value streamwhile eliminating activities (usually the majority) that don’t add value. Then the lean thinker creates aflow condition in which the design and the product advance smoothly and rapidly at the pull of the customer (rather than the push of the producer). Finally, as flow and pull are implemented, the lean thinker speeds up the cycle of improvement in pursuit of perfection. The first part of this book describes each of these concepts and makes them come alive with striking examples.
Lean Thinking clearly demonstrates that these simple ideas can breathe new life into any company in any industry in any country. But most managers need guidance on how to make the lean leap in their firm. Part II provides a step-by-step action plan, based on in-depth studies of more than fifty lean companies in a wide range of industries across the world.
Even those readers who believe they have embraced lean thinking will discover in Part III that another dramatic leap is possible by creating an extended lean enterprise for each of their product families that tightly links value-creating activities from raw materials to customer.
In Part IV, an epilogue to the original edition, the story of lean thinking is brought up-to-date with an enhanced action plan based on the experiences of a range of lean firms since the original publication of Lean Thinking.
Lean Thinking does not provide a new management “program” for the one-minute manager. Instead, it offers a new method of thinking, of being, and, above all, of doing for the serious long-term manager — a method that is changing the world.
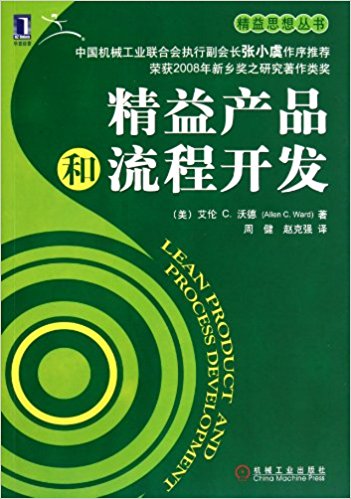
精益产品和流程开发
作者: (美)艾伦 C.沃德(Allen C.Ward)
Basic Information 基本信息
出版社: 机械工业出版社
译者: 周健 / 赵克强
出版年: 2011-4
页数: 232
定价: 38.00元
ISBN: 9787111336488
Contents 内容
内容简介 · · · · · ·
精益产品开发研究的开拓性著作
中国机械工业联合会副会长张小虞倾情作序
荣获2008年新乡奖之研究著作类奖
“企业在生产现场推行精益生产的过程中,常常会发现很多问题的根源并不一定在现场,而在“现场之上”,诸如产品设计不合理,或者是生产流程不合用。推行精益生产的团队遇到这样的问题往往一筹莫展,而技术开发部门的专家们又很少到现场参与精益的改善活动。
精益生产是制造业的一整套生产系统,而产品开发过程则是其中不可或缺的一个重要组成部分。本书确定了精益产品和流程开发系统设定的目标:创造可持续盈利的营运价值流以及创造可用的知识,非常值得企业借鉴。作者艾伦 C. 沃德博士提出了三种在开发流程中最常见的浪费:散乱失序、交接脱节和主观臆测。针对这些问题,本书提出了四个对策:
1. 建议企业聘请一位系统总工程师来领导并负责一个产品系列,包括市场、产品开发、制造以及售后服务的完整价值流;
2. 组织一个负责任的专家团队;
3. 实施多套设计方案的并行种开发;
4. 运用节拍、流动和拉动的方法来消除开发过程中的种浪费。”
作者简介 · · · · · ·
艾伦 C. 沃德博士,美国密歇根大学教授,精益产品开发研究专家。直到2004年5月飞机失事去世之前,他还在不断地对书中的思想进行完善,尝试对它们进行验证、辩论和修订。他的好朋友约翰·舒克和以及他的学生德沃德·索贝克在整理他遗作的过程中,发现了尚未出版的文稿。他们为实现沃德博士的遗志,合力将文稿整理出版,为今天学习精益产品开发贡献了一部重要著作。
译者简介:周健 博士,毕业于复旦大学管理学院,现为同济大学中国制造发展研究中心主任、机械工程学院工业工程副教授,十多年来一直从事精益生产与企业管理方面的教学、研究与咨询工作。译作有《金矿2:精益管理者的成长》,著作有《制造奇迹:格兰仕25年持续成长和全球第一的管理实践》。
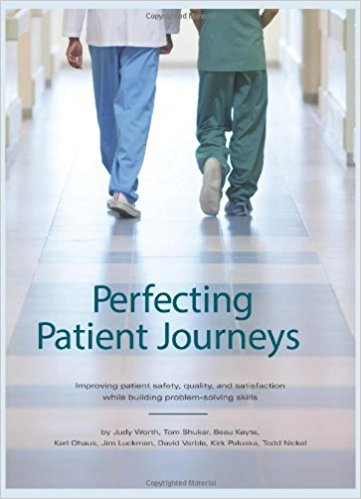
Perfecting Patient Journeys (1st Frist Edition)
by Judy Worth
Basic Information 基本信息
$30
Hardcover
Publisher: Lean Enterprise Institute, Inc. (December 17, 2012)
ASIN: B00SB3R8LM
Contents 内容
Shingo Research and Professional Publication Awardrecipient
Healthcare in the United States, and aroundthe world, is facing a crisis brought on by a combination of rising costs, lackof transparency and accountability, and preventable medical errors. Applyinglean thinking to improve care is one way that healthcare organizations canengage employees in solving problems in order to deliver better and moreefficient care.
PerfectingPatient Journeys is a guide for leaders of healthcareorganizations who want to implement lean thinking. Readers will learn how toidentify and select a problem, define a project scope, and create a sharedunderstanding of what’s occurring in the value stream. Readers will also learnto develop a shared vision of an improved future, and how to work together tomake that vision a reality.
Overthe past eight years, the authors of this book have helped healthcareorganizations learn how to make real and sustainable change using thevalue-stream improvement method. Implementing lean thinking has helpedhealthcare providers develop an adaptive, problem-solving culture with stunningresults:
ØReducedannual staff turnover by 20%
ØAveragelength of stay (LOS) in a large emergency department was reduced by 30%
ØThenumber of patients who left without being seen (LWOBS) dropped by 60% in thesame hospital
ØCustomer(patient) satisfaction increased by 73%
ØOperatingroom changeover time was reduced, which increased the number of surgicalprocedures performed by 20%
Rather than rely on huge training budgets orteams of consultants, the method described in this book focuses on solving realorganizational problems, and helps healthcare organizations and those who laborwithin them to daily provide safe, effective, efficient, and timely patient care.